Our industry is one that is constantly moving at break-neck speeds. There’s always a new product launch on the horizon. That means there’s also something to inspect. While you could certainly say quality assurance in the automotive industry is exciting, you wouldn’t describe it as easy.
What if your day-to-day work life could be a bit easier, though? As impossible as it may first sound, a Quality Liaison from Team Quality Services (TQS) is beneficial to a number of different teams within a tier 1 supplier.
Here at TQS, we provide on-site support for tier 1 automotive suppliers. Assurance in the automotive industry must be done, but it doesn’t need to be made more difficult than it has to be!
Who We Help and What We Do
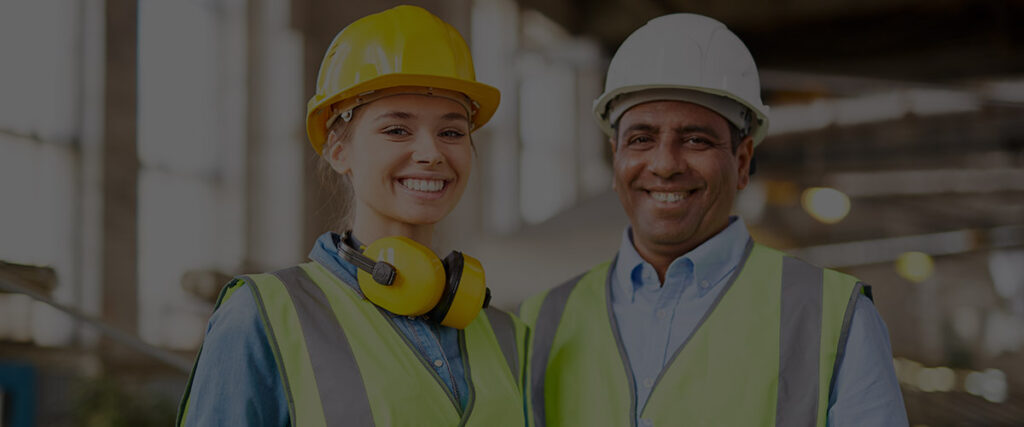
Who do we help? An easy way to answer this would be to shout “everyone!” Rather than leave the answer vague, let’s break it down a bit further. Our Quality Liaisons work with various stakeholders in the tier 1 supplier, at every part of the manufacturing process.
Our Quality Liaisons work within a wider team of professionals to ensure that the final vehicles being shipped to dealerships across the country are safe, reliable, and meet customer expectations. We do this while also keeping the entire manufacturing process as productive, effective, and cost-efficient as possible. We work alongside the design and launch team, assembly team, and the quality engineers themselves.
Design and Launch Teams
Our team works hand-in-hand with the launch team, testing to identify product durability and areas of weakness. Quality Liaisons are present to ensure that every component that goes into the assembly line in the OEM meets the quality standards. If it doesn’t, we issue a quality alert to the supplier – which we will go into further in a moment.
Quality Engineers at the Tier 1 Suppliers
Quality Engineers have enough on their plate. Our Quality Liaisons can be their representative at the OEM, working to ensure raw materials and component parts meet both companies’ quality standards.
Assembly Teams
Proper assembly cannot take place with nonconforming parts. This means the quality of the parts when they arrive at the OEM can never be in question. For the assembly teams, we’re there ensuring that supplier parts they are shipping in can be assembled properly. As well, we make sure the assembly team’s processes follow predetermined quality standards.
The Importance of an Internal Alert System
Nonconformities are inevitable, despite the best efforts of everyone involved. Rather than hoping and praying they don’t, let’s instead understand what happens when they do.
Let’s say your OEM gets a shipment of parts from you and some aren’t exactly as they should do. If you partner with TQS, we’re there to ensure that every component that goes into the assembly line in the OEM meets the quality standards. If it doesn’t, your Quality Liaison issues a quality alert to you back at the supplier. Not only do we monitor the quality of a process, we play a key role in fixing issues if and when they arise. We identify the issue proactively and handle it internally.
What if we didn’t? What if we weren’t there at the OEM to catch it? If the same quality alert comes from the OEM, you’re going to incur costs. You want us to catch it before they do! Because of the protection we’re providing, we are able to say “We’re there so you don’t have to be.”
Our Quality Liaisons are Six Sigma Greenbelt
Your Quality Liaison has a stake in your success! Our Quality Liaisons have a higher education and skill set than other comparable options within the industry, particularly when compared to inspectors from a sorting company. Our Quality Liaisons are Six Sigma certified and a Green Belt™ at minimum. This is a universally-recognized certification of aptitude in doing quality work.
This certification means an individual possesses a thorough understanding of enhanced problem-solving skills, with an emphasis on the DMAIC (Define, Measure, Analyze, Improve, and Control) model. Our Quality Liaisons have been trained in root cause analysis, among other quality standards. This enables them to have a higher level of autonomy. As a result, our Quality Liaisons ease the burden of carrying quality management responsibilities on the Quality Engineer’s shoulders alone.
We are the eyes and ears of tier 1 suppliers. Whether you’re a design and launch team, assembly team, or the engineer at the supplier, we’re here to help you! Our Quality Liaisons take pride in maintaining regular communication with you regarding your parts throughout the entire process. This is just one way we are able to drive improvements and quality assurance in the automotive industry.