A quick look at the history of the automotive industry is also a dive into the creation of quality control. Quality management in automotive started it all! While other industries were still slowly piecing together items one at a time, Henry Ford took the automotive industry to a whole new level with the invention of mass production techniques.
Brittanica tells us that Ford’s main contribution was the introduction of full-scale mass production, a process combining “precision, standardization, interchangeability, synchronization, and continuity.” No other industry could compete with how quickly and how well new cars were being mass produced, because the titan of this industry had not only production but quality down to a science.
In this same vein, the automotive industry is still ahead of other verticals in terms of technical advancements, efficiency, and quality control. If you’re not keeping up with this, you’re falling behind the competition. Your facility should make quality a main focus in everything you do. Quality management can be a make-or-break point for tier 1 suppliers.
How to Make Quality Management in Automotive a Priority
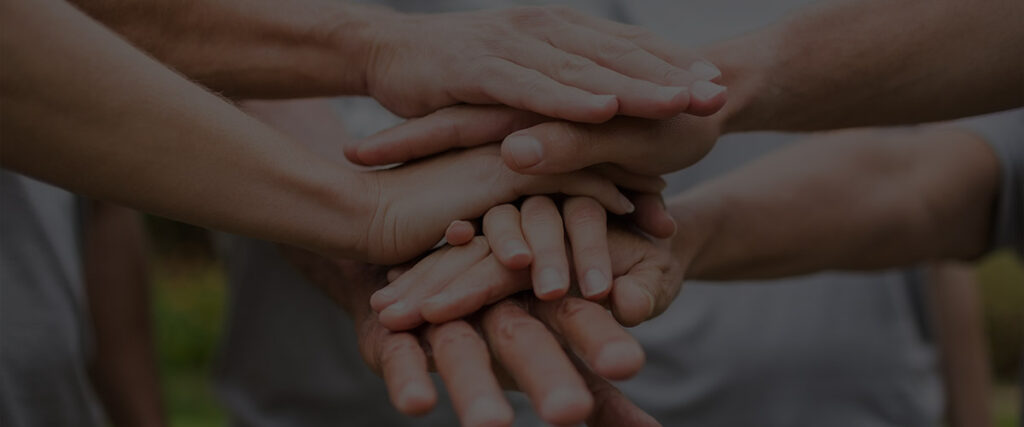
Increasing the quality of everything coming into and out of your facility is a no-brainer. When you invest in quality, you are more efficient, face less downtime, discover new growth opportunities, deal with fewer new business holds, improve customer satisfaction, and gain a competitive edge.
Overall, a focus on quality management is about improving the efficiency of your plant and achieving your business goals. The question is, how do you do it? We suggest these six ideas for improving efficiency in your plant while adhering to the highest quality standards.
#1 Bring Resident Quality Liaisons Onsite
A Quality Liaison brought in to proactively identify quality concerns is the number one thing you can do to focus on and improve quality management. You can’t be everywhere, looking at everything and everyone, all of the time.
If you partner with Team Quality Services to bring in Quality Liaisons, you don’t have to be! It’s our mission to make your job easier. Our team can cover line walks for proactive monitoring, negotiation and fault analysis when a nonconformity is found, and much more.
When you hire our team for quality support, you can expect long-term solutions for your core quality issues, increased cost avoidances, and peace of mind during production that you simply won’t be able to have otherwise. However, this is only the beginning of what we can do.
#2 Focus on Supervision and Leadership
You may feel as if you don’t need a Quality Liaison because you already have inspectors. These two are not one and the same! Inspectors sent over by a union sorting company follow a specific set of work instructions given to them by quality engineers. They are reactive. Whatever their instructions are, they do that and only that.
Sorters have a quantifiable number of parts and specific defects they’re looking for, nothing more and nothing less. When critical thinking is needed or something comes up outside of the scope of the original instructions, you need a leader on the floor.
Quality Liaisons have the ability to make decisions based on training and industry knowledge. They’re not just checking things off a list. Supervising is something we are great at! Our Quality Liaisons have a higher education and skill set within the industry when compared to inspectors from a sorting company. All of our Quality Liaisons are Six Sigma certified and a Green Belt™ at minimum. With a higher level of autonomy, our Quality Liaisons ease the burden of carrying quality management responsibilities on your shoulders alone.
#3 Use Teamwork to Your Advantage
It isn’t recommended to leave your facility’s quality management in the hands of only one person. This holds true whether that person is you or one of our Quality Liaisons. This is why we ensure you always have one of our quality management professionals onsite, even if it isn’t the same one.
For nearly all locations in North America, we have more than one Quality Liaison available. When the Quality Liaison takes a vacation, sick days, etc., you’re not left uncovered and without a path to success.
There’s always someone there, making quality management a priority. Even if the person you’re directly communicating with daily is out, you’re not without coverage. That’s our promise to you.
#4 Make Continuous Improvement High Priority
Our industry is an exciting, fast-paced one. There’s always a new product launch on the horizon. Quality management isn’t a “set it and forget it” system — or something that is established once and never addressed again.
Continually working to be more efficient with fewer nonconformities and new business holds can be the difference between putting out great products and producing unsatisfactory — or even dangerous — vehicles. Focus on ongoing improvements to maintain high quality and performance levels, regardless of market and industry changes, which vehicle you’re producing, and other variables.
#5 Emphasize a Quality-Driven Culture
One of the best ways to make sure everyone is on the same page in prioritizing quality is to make sure it’s embedded right into your company culture. You should create an environment in which all employees genuinely care about the quality of your products and how their individual work affects this.
In the automotive industry, it can be easy for your worker to focus solely on their task. Instead of focusing on each separate task, encourage your team to see the full picture and understand how they contribute to the final product’s quality. Help employees understand the importance of their contribution to quality and the company’s bottom line by:
- Clearly defining your company values
- Supporting your quality rules and guidelines with evidence
- Implementing quality training for all employees
- Setting an example of prioritizing quality for your employees
Your goals will be much more realistic and achievable if all employees are moving toward them with a unified purpose. Speaking of implementing quality culture training…
#6 Integrate Your Quality Management and Training Programs
The best time to convince your staff of their role in the quality of your final products is on day one! Begin improving your employees’ knowledge of comprehensive quality management best practices as early as possible. Incorporate your quality goals into training procedures they learn as they’re ramping up. Let new hires know that your plant takes quality very seriously.
Improving quality management in automotive is an ongoing process. We’re here to help you! Because of the more stringent qualifications that we require of our Quality Liaisons, we have a higher level of staff here at Team Quality Services. This leads to a more proficient level of communicating with you, as well as the ability to drive quality improvements. Your Quality Liaison has a stake in your success!