Benefit 1: Real-Time Information at Your Fingertips
Qnet™ allows seamless communication between you and your on-site resident engineers, bringing real-time information directly to your mobile device and web portal.
This access to real-time data provides…
- immediate visibility into the status of all locations
- instant Non-Conformance notifications
- efficient communication with resident engineers
Benefit 2: Proactive Issue Resolution
One of the key benefits of real-time field quality monitoring is the ability to receive non-conformance alerts as they happen, rather than waiting until the end of the day or the next day.
This proactive approach allows for swift problem resolution, preventing potential quality issues from escalating and impacting your production process.
Benefit 3: Data-Driven Decision Making
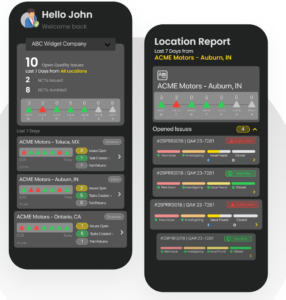
Through Qnet™, you gain access to analytics on location quality issues, savings, and part return information. This data-driven approach allows for targeted efforts towards the locations with the most quality issues, improving overall efficiency and resource allocation.
Benefit 4: Reliability and Cost Efficiency
By leveraging Qnet™, clients benefit from an efficient and reliable system for addressing quality issues, thus reducing operational costs and preventing non-conformances. Additionally, the Resident Engineer Toolkit within Qnet™ provides easy calculation of the costs associated with resident engineering efforts, allowing for informed and cost-effective decision-making.
Looking to learn more about how Qnet™ can help you and your team? See more about it by clicking the link below.