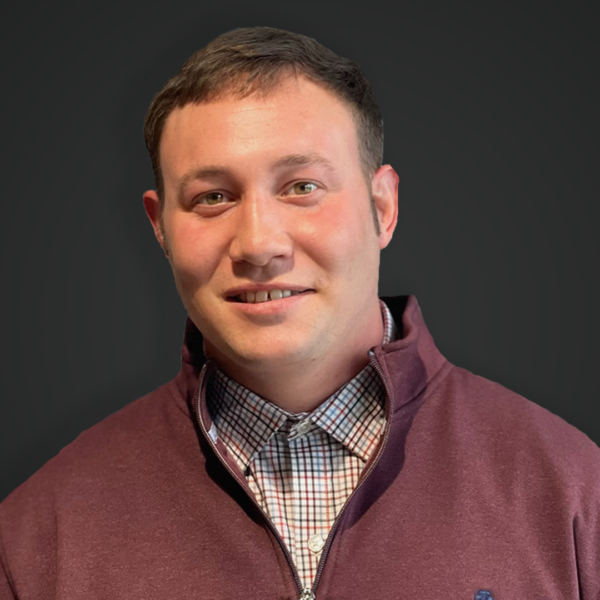
Malachi Hartley
Country
USA
About
Malachi is driven by the fast-paced environment and daily challenges of working within the OEM. He's quick to take on new parts and learn the specifics of said parts. He has a great standing relationship with plant staff and his suppliers who rely on him for his quick and detailed communication and solution-oriented mindset.
Location
Highland Park, MI, USA