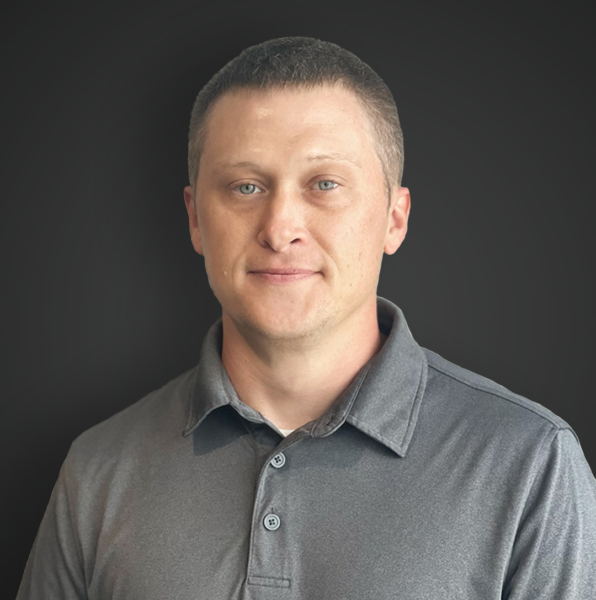
Jacob Larrison
Country
USA
About
Jacob is a highly skilled rep with hands-on experience from assembly and production to quality logistics. This has resulted in several acquired skills, including advanced problem solver and implementor of multi-platform solutions. These skills along with his diverse range of commodity specialties and established relationships with GM staff have made Jacob an exceptional performer for his customers.
Location
Springhill, TN, USA